Welcome to the first edition of Danny’s Rigging Den on Crosby’s new blog. There’s no better or more important place to start than rigging and, more specifically, the rigger.
There are many names for a rigger: slingsman, banksman, dogman, and others. Rigger is the most commonly used term worldwide and it’s also the one that best captures the work of the men and women that are among the most valuable to our industry.
Unfortunately, largely because it was not a recognized trade in the old days, riggers remain undervalued in certain regions and industry sectors. That is changing and hopefully one day it will be recognized in all four corners of the world as a trade in its own right that requires certification, or an equivalent that proves competency.
To get to that point, however, the industry must continue to raise the profile of riggers. People look in awe at the operator of a hulking crawler crane or stare in wonder at a multi-million dollar load; and, undeniably, the advancement of engineering and machinery is impressive. But think about the role of the rigger when a 1,000+ ton capacity crane has to lift a load worth in excess of $1m. You bet they should be duly-trained and recognized by all other relevant parties. With no rigger the load stays on the ground and with a bad one it gets dropped, causing costly damage or, worse, someone gets injured or killed.
It’s timely to remind ourselves of the definition of rigging, according to the US Department of Energy DOE-STD-1090-2007:
The hardware or equipment used to safely attach a load to a lifting device. The art or process of safely attaching a load to a hook by means of adequately rated and properly applied slings and related hardware.
In my opinion, most of the definitions of rigging, although sometimes close in accuracy, usually fail to capture the complete picture, across all industries effected.
I like the references to safety and rigging as an art form in the DOE’s definition. It was once consensus that just about anyone could attach a load to a lifting device using slings and various other rigging tools that one might have on hand. Yet, with the potential of injuries or deaths, how could that have been the case? This is highly skilled, demanding work; at least it is when done properly. As the lifting world gravitates to heavier capacity cranes lifting larger loads, the role of the rigger is as relevant as ever before.
We need educated craftspeople to adopt the trade and take the crane and many other industries safely into the future. By the way, I’d encourage a young person considering it to pursue a career below-the-hook. It is a great way to earn a living in the immediate term and can lead to professional development and possible advancement at many companies. Electricians, welders, steamfitters, pipefitters, etc. are recognized as serious 21st Century trades—rigging should be as well.
Rigging the art form
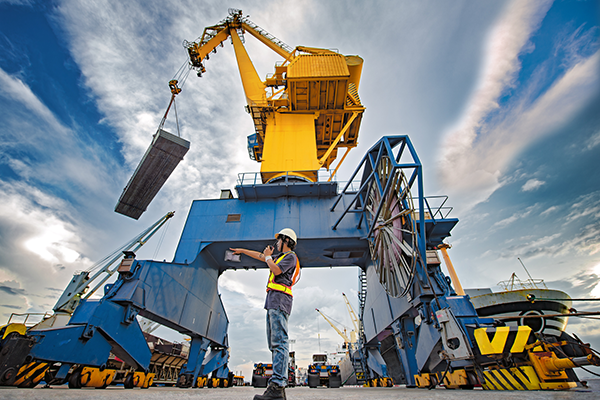
Rigging as an art form is best showcased when lifting, moving, or securing complex, critical, and/or heavy objects. Further complications are added when an item is moved over personnel or valuable equipment. When there is a requirement for multiple levels of spreader beams with snatch blocks to equalize the loading on pick points along the length of a concrete structure, for example, it takes more than a layman to complete the material handling operation safely.
The requirement for more complex rigging is on the rise. I saw a noteworthy case study recently where rigging equipment was required to lift 1,600+ tons at a span of 65+ ft. over sensitive equipment. The industry is evolving at a rapid pace. Helicopters are now utilized as lifting equipment to move loads, while other forms of transportation often require an element of securing the load to prevent unintentional movement. Rigging is often the last line of defense between success and disaster. Lives, limbs, and property are constantly at stake, only further emphasizing the need for widespread competency.
Today’s riggers must understand the regulations and standards that apply. It represents progress that there is now a better comprehension of basic, intermediate, advanced, certified, and qualified rigger competencies. At the highest level of the trade, one must have an understanding of rig planning, basic crane operations, rigging math, effects of sling angles on sling loading, D/d ratios, application / inspection requirements, and crane signaling—just for starters.
Moreover, one must understand how load control is accomplished thru the entire material handling activity. What remains the same? What changes? What are the forces being applied to the rigging equipment and load? Always remember that a load should be as stable in the air as it was on the ground.
Questions to ask before using rigging gear
Below are additional relevant questions to ask before any material handling activity with rigging gear takes place:
- Who is responsible for the rigging?
- Has communication been established?
- Is the rigging in acceptable condition?
- Is the rigging appropriate for lifting?
- Does the rigging have proper identification?
- Does all rigging gear have known working load limits?
- Are those working load limits adequate?
- What is the weight of the load?
- Where is the center of gravity?
- Is the load rigged to the center of gravity?
- What is the sling angle?
- Will there be any side or angular loading?
- Are the slings padded against corners, edges, protrusions, or abrasive surfaces?
- Is the hitch appropriate for the load?
- Is a tag line needed to control the load?
- Will the load lift level and be stable?
- Any unusual environmental concerns?
- Any special requirements?
- Do you see why this isn’t a trade that can be mastered overnight?
Really, only after being exposed to complex, critical, or heavy material load handling activities, can someone truly appreciate the difficulty and complexity of a rigger’s trade.
The rigger also does not always have the luxury of a crane to move the load and must resort to creative thinking and a good understanding of the best tools available to arrive at an optimal solution to get the object moved to its desired location.
Without riggers great swathes of factories, construction sites, refineries, shipyards, mining operations, and an endless list of other critical markets would cease to accomplish their daily objectives.
Next time you see one, give a rigger a due nod of appreciation.
Rig safe!
– Danny
Danny’s Rigging Den is a blog series written by Danny Bishop, Crosby’s corporate director of value added training.