The process of bundling and transporting tubulars in the oil and gas industry involves a high concentration of lifts. Traditionally, standard wire rope clips were used to secure the sling eye in the tight choke hitch position. However, this unconventional use of the grip raised several issues for operators.
Many low-quality wire rope clips available on the market are known to fail in this configuration, leading to the opening of the hitch and posing a potential risk of dropped objects.
When the bundles were laid down, there was a possibility for the eye of the sling to “jump” over the clip, causing the hitch to open and the slings to shift positions.
There was a significant risk of sling damage as the bearing point of the sling came into contact with the threaded area of the U-bolt and the securing nuts.
In response to a request from a major drilling contractor in the Middle East, Crosby was approached to address the issue of tubular handling and provide a solution that would mitigate the risks associated with using conventional wire rope clips for this process.

OUR SOLUTION
By aligning our global product development and engineering team with our internal forging capabilities, we successfully designed and tested several prototypes. This led to the release of the G-460/G-461 bundle clip, which has become our flagship product.
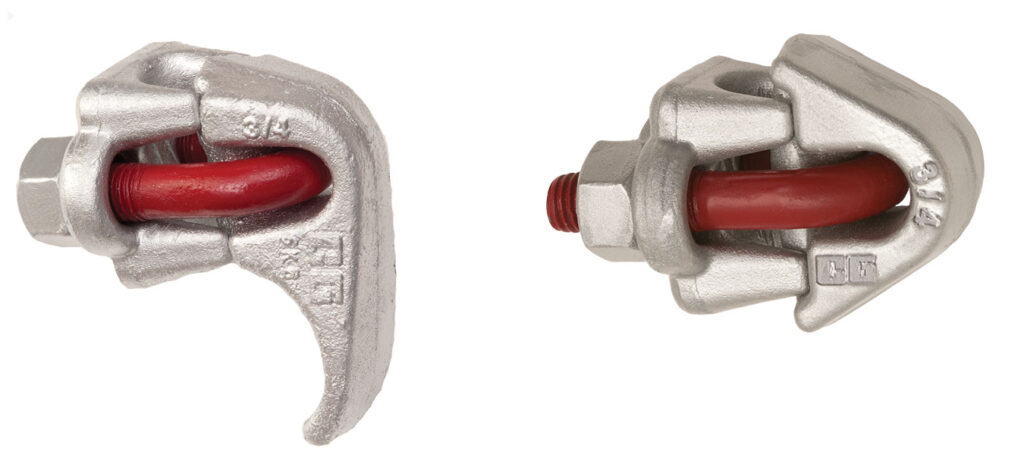
The design philosophy behind the G-460/G-461 bundle clip focused on four key factors: safety, practicality, efficiency, and affordability. These were identified as the industry’s essential requirements.
Both the G-460 (pictured left) and the G-461 (right) bundle clips were manufactured using forged materials, ensuring enhanced durability. Unlike standard wire rope clips that are single-use, our clips provided a reusable option to our clients.
The G-460 bundle clip featured a unique “finger” on the saddle, enabling the choker hitch of the sling to maintain its position and the shape of the choked bundle, even after the load tension is released. This feature made it ideal for applications such as “Shore to Ship” and “Ship to Shore,” facilitating quick and easy crane attachment without any risk of open hitches.
Additionally, the G-460 bundle clip boasted a more ergonomic profile design, ensuring a secure attachment for use with thimble eye terminations.
Our G-460/G-461 bundle clips were developed with a keen focus on meeting industry needs, and their superior functionality and durability make them a reliable choice for our valued customers.
BOTH MODELS OF BUNDLE CLIPS
Meets or exceeds all requirements of ASME B30.26, including manufacturing ID and size requirements. Importantly, these wire rope bundle clips also meet material traceability, a factor not addressed by ASME B30.26.
Are supplied fully galvanized to mitigate the effects of rust and corrosion present in the harsh offshore environment.
Each base and bundle clip adapter has a product identification code (PIC) for material traceability, the name Crosby or CG, and the nominal wire rope size forged into it.
Originally designed for 3/4” wire rope, the transition into deeper drilling and larger tubular sizes prompted the need to produce them for 3/4” and 7/8” wire rope.
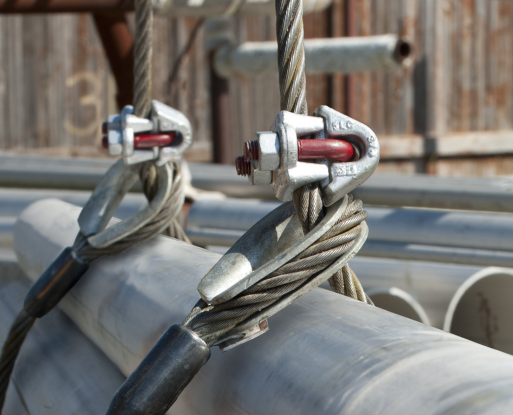
VALUE TO THE CUSTOMER
The introduction of the G-460 and G-461 model clips has significantly reduced the incidents that were previously common when using standard wire rope clips for this application. Feedback from our original client and major drilling contractors who have now adopted the use of the G-460/461 model clips include:
- Enhanced safety and performance
- Lifting operations conducted with a clip specifically designed for this purpose, promoting the best industry practices
- Decreased operational time on-site for resetting hitches, resulting in reduced crane costs
- Long-term cost savings in materials
- Improved traceability and certification levels compared to standard wire rope clips available on the market
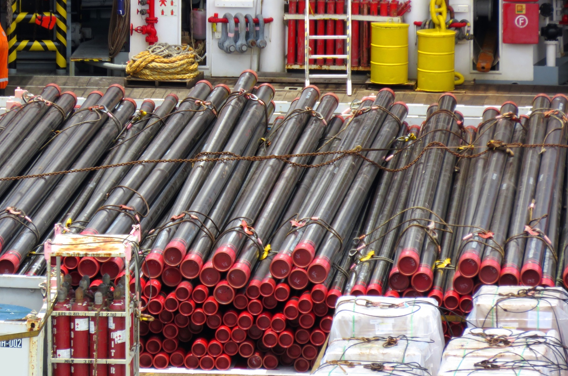